- 工厂自动化技术概述
- • 工厂自动化发展史
- • 工厂自动化概念
- • 工厂自动化的主控系统
- • 综合自动化的基础配套元件
- • 综合自动化的系统结构
- • 工厂综合自动化的成果
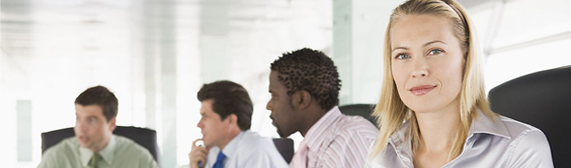
工厂自动化技术概述
20世纪40年代开始, 人們开始使用分散式测量仪表和控制装置, 进行单参数自动调节, 取代了传统的手工操作。
  50 年代,人们开始把检测与控制仪表集中在中央控制室, 实行车间集中控制, 一些工厂企业初步实现了检测仪表化和局部自动化.这一阶段, 过程控制系统结构绝大多数还是单输入单输出系统, 受控变量主要是温度、压力、流量和液位四种参数, 控制的目的是保持這些参数的稳定, 消除或减少对生产过程的干扰影响.而过程控制系统采用的方法是经典控制理论中的频率法和轨迹法, 主要解决了单输入单输出系统的常值控制和系统综合控制问题.
  60 年代, 工业生产的不断发展, 工厂自动化程度大大提高。在自动化仪表方面, 开始大量采用单元组合仪表.为了满足定型、灵活、多功能等要求, 还出现了组装仪表, 以适应比较复杂的模拟和逻辑规律相结合的控制系统需要.与此同时, 开始采用电子计算机对大型设备, 如大型蒸馏塔、大型轧钢机等, 进行最优控制, 实现了直接数字控制(DDC)及设定值控制(SPC)。在系统方面,出现了包括反馈和前馈的复合控制系统。在过程控制理论方面, 除了仍采用经典控制理论解决实际生产过程中的问题外, 现代控制理论也开始得到应用, 控制系统由单变量系统转向复杂的多变量系统.在此期间, 工厂企业实现了车间或大型装置的集中控制.
  70—90年代, 现代工业生产的迅猛发展, 自动化仪表与硬件的开发, 微计算机的问世, 使生产过程自动化进入了新的高水平阶段。对整个工厂或整个工艺流程的集中控制, 应用计算机系统进行多参数综合控制, 或者用多台计算机对生产过程进行分级综合控制和参与经营管理, 是这一阶段的主要特征。在新型自动化技术工具方面, 开始采用微机控制的智能单元组合仪表, 显示和调节仪表, 以适应各种复杂控制系统的需要.现代控制理论中的状态反馈、最优控制和自适应控制等设计方法和特殊控制规律, 在过程控制中得到了广泛应用, 自动化技术呈现出一派欣欣向荣的新景象.
 
进入21世纪以来,“以人为本”、“节能环保”的观念深入人心,对工厂自动化提出了新的要求。随着计算机技术、无线技术、现场总线技术、工业以太网技术、IT技术、机器人技术,传感器技术以及安全技术等科学技术的不断发展与创新,工厂自动化在经历了单机自动化、车间自动化、全厂集中控制等几个重要 阶段之后正向工厂综合自动化 (又称全盘自动化)发展,即把过程控制.监督控制 、产品设计 、质量监测 、工厂管理等方面融为一体,运用现代控制理论 . 大 系 统 理论、人工智能、4 C ( Co mp u t e r 、Co mmu -I 1 i e a t i o n、CRT、Co n t r o 1 )技术,实现优化控制、分级控制、 分散控制 、测试自动化、建筑物自动化、信息处理与经营决策 自动化, 以便进一步提高工作效率,保证 质量与安全,节约能源和原材料。
  化工厂实现综合自动化,可 以保 证化学反应达到最佳,自动配料,对成品质量进行自动监测,仓库 自动化管理,适应化工产品向多品种小批量的过渡。
工厂自动化是指用自动装置或系统控制來管理生产设备及生产过程, 它集计算机技术、自动化技术、激光技术和机器人技术之大成。一般认为, 工厂自动化是指利用计算机充分掌握从接受订货开始, 到产品发货结束之间所有生产活动的复杂信息流,并对生产系统整体进行高度管理和控制的自动化过程.其目的主要是: ①省力;②提高设备运转率和利用率;③实现高效生产管理, 即减少零件、材料、半成品和成品的库存量、减少资金积压, 加快资金周转, 创造大的经济效益;①缩短从产品规划、设计、研制到产品出厂之间的生产周期;⑤满足用户对产品的多样化、多功能化和智能化需求。
工厂自动化, 按其性质又可分为连续生产自动化和断续生产自动化两种。连续生产自动化又叫过程自动化, 主要是指石油、化工、冶金、电力等工业部门中连续生产过程的自动化.即通过采用各种检测仪表、调节仪表、控制装置、电子计算机等自动化技术工具, 对整个生产过程进行自动检测、监督和控制, 以达到实现各种最优的技术经济指标, 提高经济效益和劳动生产率, 节约能源、改善劳动条件、保护生态环境等目标。
一个实现自动化的工厂,应具有以下特征:
第一 就是有一个内部联网的现代化的信息管理系统,即通过网络实现全厂生产、信息采集与处理、财务、人事、技术与设备等的计算机自动化管理;
第二 就是生产设备实现自动化,即单个设备由计算机控制,生产过程中实现自动传输等;
第三 就是建成一个“柔性生产系统”,即具备一种新型的多品种、少批量生产的加工设备。这种系统比较容易适应设计的改变和加工物形状、数量的变化。这种系统可大可小,大的由若干控制装置、监控电脑、机器人及无人运输车组成,可以构成整条生产线;小的则可以独立完成各种各样的加工生产任务;
第四 就是产品设计与生产工艺设计实现自动化,并采用了计算机辅助设计的方法,这样既节省了设计时间和费用,又大大提高了生产效率;
第五 就是建立了自动化仓库,实现工厂自动化的一个必备的条件。对一个工厂的原材料、半成品和成品实现自动化管理,不仅能提高场地的利用效率,减少管理费用,还能使物品的存取变得井然有序,一旦某种生产原料告缺,采购部门将立即从中获得信息,及时进货。
一个自动化工厂的主要表现就是:生产线上的人员减少到最低限度,除少数的维修人员外,生产线上的整个生产过程几乎不需人员参与,可以一天24小时连续不停地生产,产品的质量稳定可靠,生产效率也很高。
工厂综合自动化要求实现的控制功能,主要是由分散型控制系统( DCS ) 完成。 DCS主要采用4 C技术 。把信息采集、过程控制、能源监测, 监督控制、 管理调度有机地结合起来 ,通过通讯网络渗透到工厂的每一个环节,成为工厂自动化的主控系统。目前DCS正在向 以下几个 方面发展:
1 .采用 高速 、中速、低速通讯技术,发展装置型和仪表型等多种结构形式,构成完整的控制体系,既可组成大规模的分层分散管理与控制系统,又可组成中小规模的分散型控制系统。
2 .采用国际公认标准或规程( 如MAP 或MI NI MAP等),把现场使用的不同机型 联结起来,共同构成统一的综合自动化开放系统,从而尽量降低对具体机型的种种限制。
3 .把基本控制器、可编程控制器,分批控制器和单、多回路控制单元进行系列化设计,使之成为一个统一的 “ 家族”, 以适应连续生产过程,断续生产过程、分批生产过程控制的要求。
4 .大力开发软件,应用专家系 统,不断增强DCS 的控制功能和管理功能,提高信息处理和管理调度水平,优化DCS 的应用效果。
5 .开展可靠性设计,强化自诊断功能,采用表面安装新工艺, 以便提高系统的整体可靠性和安全性。
除上述主控系统以外,还有多种传感器、变送器、检测仪表、显示仪表和执行器,这些都是工厂自动化的基础配套元件,这些元件也在不断发展和完善中。工厂自动化需要获得大量信息,包括热工量 ( 温度、压力、流星、物位等),电工 量 ( 电压、电流、功率、频率等),化学量 ( O2 、CO、CO2 、CH4 、P H、离子等) 。物理量 ( 光、声、磁、湿度、浊度等),状态量 ( 一维、二维等) 。
生产管理的各个环节,即从币场分析、产品设计、加工制造、经营管理、售后服务的全部生产活动是一个不可分割的整体,是紧密关联,要统一考虑:
全部生产过程实质上是一个数据采集.传递和加工处理的过程.最终形成的产品可看作是数据的物质表现.把孤立的,局部的自动化技术和子系统,在新的管理模式与工艺指导下,综合运用信息技术,自动化技术。并通过计算机及其支持软件灵活而有机的综合起来.构成一个完整的系统.对生产过程的物资流,管理过程的信息流和决策过程的决策流进行有效的控制和协调.以适应新的竞争模式下市场对生产和管理过程提出的高质量、高速度、高灵活和低成本的要求.
工厂综合自动化的系统结构采取集中与分散相结合的模式,以集中管理、统一决策为前提,以分散控制 、信息分区处理为基础,以通讯网络为集中管理与分散控制的联 络手段。? 对 于连续生产过程的综合自动化,重点采用CI PS( 或PCI M)的系统结构, 以DCS和PLC 为主控系统, 在单机自动化,车间自动化的基础上向分级分层控制系统发展,并将 CAD、仓库自动化、包装自动化、 能源监控、通用数据库、管理信息系统纳入体系 。
工厂综合自动化的功能包含着工厂的全部生产经营活动.即从市场预测 产品设计 加工制造,生产管理.到售后服务的全部活动.比传统的工厂自动化范围要大得多.是一个复杂的大系统, 全厂一体化控制并非只是工厂各环节自动化的简单相加.而是把企业全部生产经营活动视为一个 整体.就是把企业内相互分立的技术 (如 C A D, C A M… ) 和人员(各层次)通过计算机有机的结合起来.使其能快速、灵活,准确和协调地进行。
制造业的生产过程可简单地分为设计、制造和管理三大部分.早期的自动化只是其中某一活动的自动化.计算机的应用使自动化从单项扩展到局部.如生产加工中心、工业机器人 计算机辅动工程,统计和财务管理等.现在的工厂一体化控制将自动化从局部扩展到全体.从刚性自动生产线发展到柔性自动化生产线将工厂自动化向深度和广度推进.使企业增强了竞争力.获得了显著效益。
工厂综合自动化系统包括:
1、集成管理信息系统:
包括外部的需求( 市场预测 订单和原材料供应)到内部的设备、人力、财务生产、库存管理以及成本、质量,经营计划等。
(1)物料管理系统(MM):包括材料消耗定额,材料供应计划 物料供应、采购,库存等.
(2) 生产管理系统(PM) .包括生产准备计划、编制、生产作业计划编制,作业计划控制、车间设备能力 、工时管理等。
(3) 质量管理系统(QC):包括质量法规 、质量检验规程、 器材质量检验 、生产 过程质营量控制、计量器具,标准化信息、人员资质及培训等。
(4) 财物管理系统(FM) 包话财务、工资、资金资产以及专用资金、产品销售价格、产品成本,会计报表 合周管理等方面的管理,分析和预测。
(5) 人力资源管理系统(MP):包括人事 劳资 培训教育 员工健康档案,人员技术素质等。
(6) 经营计划管理(BM);包括生产经营状态信息 经营计划,合同管理市场规划、订货状况、售后服务.总经理办公系统和经营决策支持系统等。
2、柔性制造工程 (FME)
主要有单元作业、调度系统.系统运行状况监控,检测? 人力智能和各种设备等的物流系统.
( 1 ) 单元管理信息系统:包括库存 监测自动化管理 生产准备和调度计划营理.以及人工智能和模拟仿真等。
(2) 物流系统:包括数控加工、测量、维护等设备。自动化仓库与物品流动,物资自动传递等设备。
3、数据库和网络:
上述各系统的信息数据都要在一个容量足够大而结构合理的数据库系统里存储和调用,为了确保信息畅通.还必须制定统-规范和通信协议.以便将不同规格的设备组网和交流信息。
据美国科学院对麦道飞机公司、迪尔拖拉机公司,通用汽车公司、西屋公司和英格索尔铣床公司等五家企业的调查分析 。采用全厂一体化控制获得如下效益:产品质量提高 2— 5倍 、生产效率提高 40— 70% 、设备利用率提 着 2—3倍 、生产周期缩短30一 60% 、工程师的工作能力提高3— 35倍。
联系我们
》QQ: 2540402053
》skype: kingsunservice
》mail:kingsun_sales@126.com